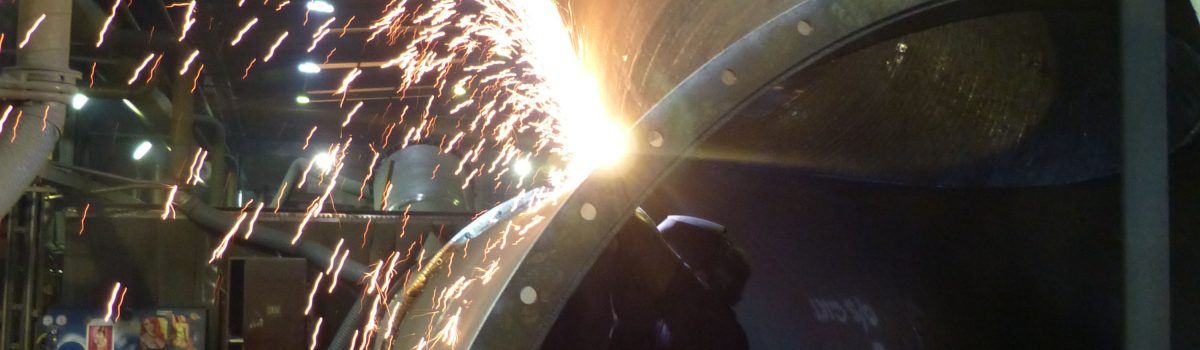
Fabrication Services
Fabrication and refurbishment expertise
As a major manufacturer of overlay wear resistant plate, Red Dog Linings has in-depth knowledge of the physical and mechanical characteristics of such material. This enables us to recommend the most appropriate fabrication technique and select the optimum weld bead orientation for applications in which material flow is a factor. Similarly, we can offer special low friction finishes for adhering (sticky) materials of ‘captured material’ techniques for severe environments.
The Red Dog Linings’ workshop has developed extensive experience in the profiling, forming, and fabrication of T200X ™ hardfaced plate into complex shapes including curved and conical sections. These can have T200X ™ hardfacing alloy facing on either the inside (pipe work and reduction services) or the outside (classifier cones and externally clad pipe).
Red Dog Linings Limited is the sole manufacturer of our proprietary T200X ™ hardfacing wear resistant materials. We have major fabrication facilities at our manufacturing headquarters in the UK. Red Dog Roll Reclamation, which is part of Red Dog Linings Group, is a leading specialist in the manufacture and refurbishment of hardfaced rolls for steel mills, food manufacture, and other industries. It also undertakes a wide range of general engineering projects such as the manufacture and repair of roll bearing housings, including heavy duty chocks, roll end furniture, drive shafts, and spindles.
Current plant
Red Dog Linings has fully equipped and integrated workshop facilities capable of the manufacture and fabrication of T200X ™ Hardfaced plate, roll manufacture and refurbishment, as well as a wide range of refurbishment of industrial plant items which involves general engineering, machining, and fabrication skills all available under one roof.
Our facilities include:
Profiling
- Viper CNC hi-def plasma profiling with True Hole technology
- Cutting dimensions up to 8000mm x 3000mm x 40mm
- Orbital tool head for countersinking and edge chamfering
- Oxyfuel cutting up to 150mm thickness
- 2D CAD input including DXF formats
CNC plasma
- with orbital tool head for countersinking and edge chamfering
- Cutting dimensions 3500mm x 3000mm
- Hand plasma and oxyacetylene burning torches
Forming
- Press brake 250 tonne capacity producing corners, cones and bends
- Forming rolls bending up to 200 tonne capacity
- Cone rolling – up to 30mm thick
Straightening rolls
- Flattening up to 30mm thick plate
Welding
- 21 sets of 600 Amp water-cooled MIG sets manual and semi-automatic processes
- Welding – 11 MMA sets
- TIG welding
- Pressure testing equipment
Positional equipment
- Manipulators ranging from 1 tonne to 40 tonne
- Powered tank rolls from 1 to 20 tonne
- 2 axis manipulators – 2, 3, 5, 10 and 40 tonne capacity
Overhead crane
- All workshops are served by two adjacent 10 tonne overhead cranes
- with a maximum straddled lift of 18 tonnes
Transport
- HGV rigid body capacity 16 tonne
- Ford Transit pickups – 2 off x 1 tonne